Drilling fluid, commonly known as “mud,” is critical to the success or failure of the mud circulation system. Typically stored in mud tanks on onshore and offshore drilling platforms, these tanks serve as the hub of the mud circulation system, with their fluid levels directly impacting system safety, efficiency, and costs.
The system pumps drilling fluid through the drill pipe to cool and lubricate the drill bit. Then the mud flows back to the surface, carrying formation cuttings. The fluid level in these mud tanks is measured by inline level sensors or inline level transmitters, which provide critical data for drilling operations. The system monitors the total volume of mud to find net gains or losses. Any increase of drilling fluid indicates the influx of external substances like oil, water, or gas into the drilling process, while a decrease suggests loss into the formation. Both scenarios are extremely hazardous and could lead to a blowout.
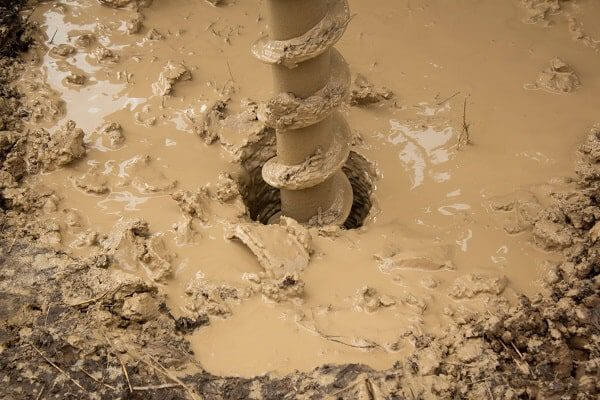
1. Drawbacks of Traditional Fluid Level Monitoring
Traditional level measurement of drilling fluids faces challenges in personnel safety, delayed responses and hidden cost. Let’s dive into those three negative effects.
Safety hazards come as the fatal drawback of manual level monitoring in continuous drilling operation. Mud tanks are 3 to 5 meters high in general, and observers need to climb to the slippery or windy top of tanks, which can lead to falls due to slippery surfaces or strong winds. Moreover, Open observation ports may release hazardous gases such as hydrogen sulfide (H₂S) or methane (CH₄), posing health risks to personnel.
Limited monitoring frequency (1-2 times/h) and delayed response are two reasons of neglects in sudden level changes like rapid rises or drops during lost circulation or well kicks. It’s estimated that manual level monitoring during a single well’s drilling consumes over 50 hours, equivalent to wasting 2–3 days of effective operational time. Furthermore, 5–10 minutes later feedback to the driller lead to mud overflow or pump cavitation in case mud levels near the upper or lower limits.
Inaccurate manual control is liable to overflow incidents, in which dozens of cubic meters of drilling fluid may be wasted in a single event. Extreme low fluid levels may cause idling operation of pumps and further maintenance cost for equipment wear.
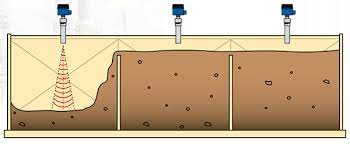
2. Recommended Solutions for Inline Fluid Level Monitoring
Modern intelligent automation systems for real-time level monitoring combines technology upgrades with aggregate monitoring systems. Free data transmission through cables and wireless mode to end monitor enables real-time monitoring through curve graphic of fluid levels and alarms for high & low limits. For example, red flashing is the reminder of fluid level over 90% or lower than 10%.
(1) Radar Level Sensors (Non-Contact)
Radar level transmitters are suitable for high-viscosity, foam-prone drilling fluids (e.g., oil-based mud), unaffected by medium fluctuations. They measure fluid level by emitting high-frequency electromagnetic waves and calculating the time difference of reflected signals.
In deep drilling platform mud tank groups, radar sensors penetrate steam and mist to monitor tank levels in real time, integrating with mud pumps to automatically adjust flow rates. Explosion-proof design (compliant with ATEX and IECEx standards), ideal for high-risk environments like sulfur-containing oil and gas wells.
(2) Ultrasonic Level Sensors (Non-Contact)
Ultrasonic level transmitters are ideal options for small-to-medium drilling teams at a comparative low cost, measuring fluid level by emitting ultrasonic waves and calculating echo return times. It’s easy to install by thread or flange connection a maintenance-free period of up to 12 months. It’s susceptible to interference from steam or dust, best suited for cleaner water-based mud tanks.
3. Intelligent and Collaborative Monitoring
Combining inline level sensors with inline density meters and inline temperature transmitters to create a comprehensive mud performance monitoring system. For example, a sudden level drop combined with a density spike triggers automatic identification of lost circulation, initiating emergency sealing procedures.
Edge Computing and AI Prediction:
Machine learning analyzes historical level data to predict mud consumption trends (e.g., accelerated level drops when drilling into specific formations), enabling proactive mud reserve scheduling to reduce downtime risks.
Remote Operations:
Oilfield headquarters can monitor mud tank levels across multiple well sites in real time via cloud platforms, enabling unified resource allocation and “multi-well collaborative management,” particularly for cluster well development.
Mud tank level monitoring has evolved from a labor-intensive task to a technology-intensive one driven by industrial IoT technology reshaping traditional operations. Inline level sensors are not merely measurement tools but critical nodes connecting drilling safety, efficiency, and costs. For oil companies pursuing high-quality development, adopting intelligent monitoring solutions is both a critical need to reduce safety risks and a strategic investment to enhance competitiveness in an industry downturn.
Obtain a customized level monitoring solution! Click to contact us and unlock the next efficiency growth point for smart drilling.
Post time: Jun-05-2025