Perfect beer originates from precise control over the brewing process, particularly during wort boiling. The wort concentration, a critical parameter measured in degrees Plato or specific gravity, directly impacts fermentation efficiency, flavor consistency, and final product quality. For large-scale breweries, maintaining optimal wort concentration is not just a matter of quality but also a key factor in operational efficiency and cost management. A wort concentration meter, wort concentration monitor, or wort concentration analyzer provides real-time data to ensure consistency, reduce waste, and meet regulatory standards.
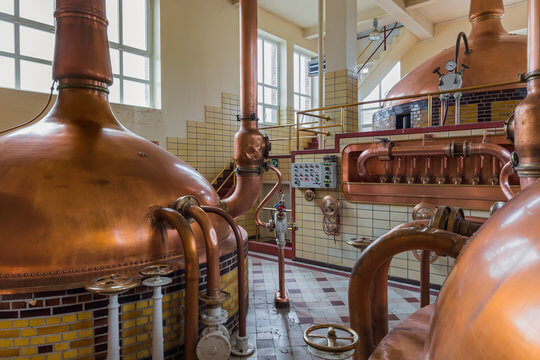
Applications in Brewing
Wort boiling is a critical step in brewing, performed in a wort pan or with an external boiler (shell or plate heat exchanger), lasting 50–75 minutes per brew. The objectives include:
- Adjusting Wort Concentration: Evaporating water to achieve the desired wort strength.
- Inactivating Malt Enzymes: Denaturing enzymes to stabilize wort composition.
- Fixing Wort Composition: Setting the chemical profile for consistent fermentation.
- Sterilizing Wort: Eliminating microbial contaminants for a clean fermentation process.
- Coagulating Proteins: Promoting protein precipitation to improve clarity and stability.
- Isomerizing Hops: Converting hop alpha acids into bitter, soluble iso-alpha acids.
- Developing Flavor: Creating characteristic flavors through chemical reactions.
- Removing Undesirable Volatiles: Evaporating off-flavors like dimethyl sulfide (DMS).
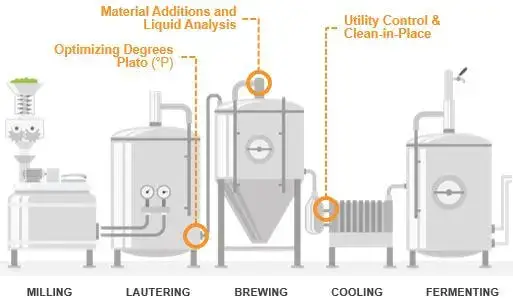
Why Wort Concentration Matters in Brewing
The Role of Wort Concentration in Beer Quality
Wort concentration refers to the amount of dissolved solids, primarily sugars, in the wort. Measured using tools like a wort concentration meter, this parameter determines the original gravity (OG), influencing alcohol content, mouthfeel, and flavor profile. Water evaporates, concentrating sugars and other compounds are ought to subjected to recipe specifications.
Inconsistent wort concentration can lead to off-flavors, poor fermentation, or deviations from target alcohol levels, all of which can compromise product quality and brand reputation. For large-scale breweries, where even minor variations can result in significant financial losses, using a wort concentration analyzer ensures every batch meets exact standards.
Challenges of Inconsistent Wort Concentration
Factors like boil duration, heat intensity, or equipment inefficiencies can cause fluctuations in wort concentration. Traditional manual sampling is time-consuming and prone to human error, especially in high-volume production. These inconsistencies can lead to costly reworks or discarded batches.
Additionally, regulatory bodies often require precise documentation of brewing parameters, making automated solutions like a wort concentration monitor indispensable for compliance. By integrating real-time measurement tools, breweries can address these challenges, ensuring uniformity across batches and minimizing waste.
How Wort Concentration Meters Work in Brewing
Technology Behind Wort Concentration Measurement
A wort concentration monitor typically uses advanced technologies such as ultrasonic velocity or density measurement to determine the concentration of dissolved solids in real time. These devices are installed inline within the brewing system, allowing continuous monitoring during wort boiling.
Integration with Brewing Systems
Modern wort concentration analyzers are designed to integrate seamlessly with automated brewhouses. They connect to control systems, providing real-time data to programmable logic controllers (PLCs) or brewery management software. This integration enables brewers to monitor and adjust parameters like boil intensity or evaporation rate instantly. For instance, if the wort concentration is too low, the system can extend Boil time or increase heat input, ensuring the target gravity is achieved without manual intervention. This level of automation is critical for large-scale breweries aiming to maintain efficiency and consistency.
Best Practices for Controlling Wort Concentration During Boiling
Optimizing the Wort Boiling Process
Boiling the wort is a pivotal stage where wort concentration is adjusted through evaporation and hop addition. To achieve optimal results, breweries should follow these best practices:
- Monitor Boil Parameters: Use a wort concentration analyzer to track evaporation rates and sugar concentration in real time. Adjust heat input or boil duration based on live data to avoid over- or under-concentration.
- Calibrate Equipment Regularly: Ensure the wort concentration meter is calibrated to maintain accuracy, especially during extended production runs.
- Control Hop Additions: Hops can affect wort viscosity and measurement accuracy. Schedule additions strategically and account for their impact when monitoring wort concentration.
- Maintain Equipment: Clean and inspect boiling kettles and sensors to prevent residue buildup, which can skew readings.
By implementing these practices, breweries can maximize the effectiveness of wort boiling and achieve consistent results.
Data Visualization for Process Control
Large-scale breweries benefit from integrating wort concentration monitors with data visualization tools. Real-time dashboards can display key metrics like Plato, specific gravity, or evaporation rate, enabling brewers to identify trends and make informed decisions. For example, a line graph showing wort concentration over time can highlight deviations, prompting immediate adjustments. These tools align with the content preferences of large-scale breweries, which prioritize quick access to actionable insights.
Addressing Common Issues in Wort Boiling
During wort boiling, several issues can affect wort concentration, including foaming, scorching, or uneven heat distribution. A wort concentration analyzer helps mitigate these by providing early warnings of anomalies. For instance, excessive foaming may indicate over-concentration, while scorching can alter sugar profiles, both detectable through real-time monitoring. By addressing these issues promptly, breweries can maintain product quality and reduce waste.
Recommended Lonnmeter Wort Concentration Meters
Lonnmeter specializes in inline measurement solutions, leveraging technologies like ultrasonic and density-based methods to deliver accurate and reliable wort concentration data. Their wort concentration meters are engineered for seamless integration into brewhouse systems, offering real-time feedback during wort boiling to ensure precise control over sugar content (measured in degrees Plato or specific gravity). These devices are designed to withstand the harsh conditions of brewing environments, including high temperatures and corrosive wort, making them ideal for large-scale operations.
Alignment with Brewery Needs
Large-scale breweries prioritize efficiency, cost savings, and compliance, as outlined in your preferences. Lonnmeter’s wort concentration analyzers address these by offering automated, maintenance-free solutions that integrate with PLC or DCS systems via 4-20mA or RS485 protocols. Their hygienic design meets food-grade standards, ensuring safety and quality in beer production.
Key Benefits for Large-Scale Breweries
Real-time monitoring with a wort concentration analyzer transforms the brewing process by providing instant feedback during boiling wort. Unlike traditional methods, which rely on periodic sampling, inline systems deliver continuous data, allowing brewers to adjust parameters on the fly. This capability is particularly valuable for large-scale breweries, where production runs are extensive, and downtime is costly. Key benefits include:
Precision and Accuracy: Lonnmeter meters provide high-resolution measurements (e.g., ±0.05% Plato), ensuring consistent wort concentration across batches.
Real-Time Monitoring: Inline sensors eliminate the need for manual sampling, reducing labor costs and errors.
Durability: Constructed with robust materials like stainless steel or titanium, these meters are built for long-term use in demanding brewery settings.
Compliance Support: Accurate data logging facilitates regulatory reporting, aligning with standards.
Cost Efficiency: By optimizing boiling the wort, breweries can minimize raw material waste and energy costs.
Common Questions About Wort Concentration Control (FAQ)
What Is the Ideal Wort Concentration for Brewing?
The ideal wort concentration varies by beer style but typically ranges from 8–20° Plato for most ales and lagers. A wort concentration meter ensures the wort reaches the target gravity, which is critical for achieving the desired alcohol content and flavor profile. Brewers should consult recipe guidelines and use real-time monitoring to maintain consistency.
How Does a Wort Concentration Monitor Improve Efficiency?
A wort concentration monitor provides continuous data during wort boiling, eliminating the need for manual sampling. This reduces labor costs, minimizes errors, and allows for immediate adjustments, improving overall efficiency and reducing waste in large-scale operations.
Can Wort Concentration Analyzers Be Used for Other Beverages?
While primarily designed for beer, wort concentration analyzers can be adapted for other fermented beverages like cider or mead, where sugar concentration impacts fermentation. The same principles of real-time monitoring apply, ensuring consistent quality across production.
Controlling wort concentration in brewing is a critical step for large-scale breweries aiming to deliver consistent, high-quality beer while optimizing efficiency and compliance. By integrating advanced tools like a wort concentration meter, wort concentration monitor, or wort concentration analyzer, brewers can achieve real-time precision during wort boiling, reducing waste and ensuring every batch meets exact specifications. These systems not only enhance product quality but also streamline operations, making them indispensable for high-volume production. To explore how a wort concentration analyzer can transform your brewing process, contact a trusted supplier Lonnmeter today for more information on advanced brewing solutions. Take control of your wort and elevate your brewery’s performance now!
Post time: Jun-30-2025