Titanium Dioxide (TiO2, titanium(IV) oxide) serves as a key white pigment in paints and coatings, and as a UV protectant in sunscreens. TiO2 is manufactured using one of two primary methods: the sulfate process or the chloride process.
The TiO2 suspension has to be filtered and dryed. In this posttreatment a continous process monitoring by TiO2 suspension density measurement is needed to guarantee high product quality and to make up optimum use of the plant capacity. Precision is paramount in ensuring the consistent quality of titanium dioxide solution.
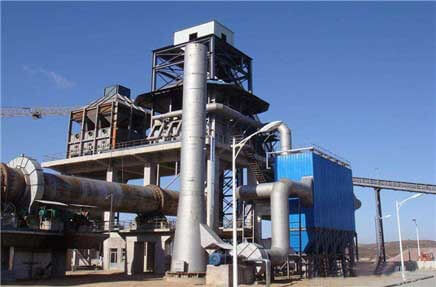
Why Density Matters in Titanium Dioxide Post-Treatment
The production of TiO2 involves complex processes, typically the sulfate or chloride method, followed by post-treatment stages such as surface coating, milling, and drying. During these stages, TiO2 is often handled as a suspension, where the density of titanium dioxide solution directly impacts the final product’s properties, such as gloss, whiteness, and durability. Variations in density can lead to inconsistent coating application or filtration issues, resulting in defective products and increased costs.
A titanium dioxide density meter provides real-time data on suspension density, allowing manufacturers to adjust process parameters instantly. By maintaining precise control over the titanium dioxide solution, producers can ensure uniformity in particle size and surface treatment, which are critical for meeting industry standards. For instance, in paint production, consistent density ensures optimal pigment dispersion, enhancing color and coverage quality.
Challenges Without Inline Density Monitoring
Without proper density monitoring, manufacturers face several challenges. Manual sampling, while common, is time-consuming and prone to errors, leading to delays in identifying density deviations. These inconsistencies can cause issues like clogged filters, uneven coatings, or reduced product shelf life. Moreover, manual methods cannot provide the continuous feedback needed for dynamic process adjustments, resulting in inefficiencies and higher operational costs. Implementing a titanium dioxide density sensor addresses these challenges by offering automated, real-time monitoring, minimizing human error, and optimizing production throughput.
Types of Lonnmeter Density Monitoring Solutions for TiO2
Vibrating tube density meters are among the most widely used tools for monitoring the density of titanium dioxide solution. These devices operate by measuring the frequency of a vibrating U-shaped tube filled with the TiO2 suspension. The frequency changes inversely with the density of the solution, providing accurate, real-time measurements.
Titanium dioxide density sensors based on ultrasonic technology offer a non-invasive solution for density monitoring. These sensors measure the speed of sound waves through the TiO2 suspension, which correlates with its density. Ultrasonic sensors are particularly effective for high-concentration slurries, as they are unaffected by the opacity or color of the solution.
Coriolis density meters provide a dual function, measuring both density and mass flow, which is advantageous for TiO2 manufacturers seeking comprehensive process control. These meters use the Coriolis effect, where the vibration of a tube is altered by the flow and density of the suspension. Their ability to handle a wide range of density levels makes them versatile for various stages of TiO2 production, from storage tanks to filtration systems.
Benefits of Inline Density Monitoring for TiO2 Manufacturers
Enhanced Product Quality
Using a titanium dioxide density monitor ensures consistent density throughout the post-treatment process, directly impacting product quality. For instance, maintaining optimal density during surface coating prevents issues like particle agglomeration, which can degrade the pigment’s performance in end-use applications. Real-time adjustments based on density data ensure that the TiO2 meets stringent quality standards, enhancing its market competitiveness.
Cost Efficiency and Waste Reduction
Inline density monitoring reduces operational costs by minimizing waste and optimizing resource use. By detecting density deviations instantly, manufacturers can adjust the concentration of the titanium dioxide solution before defective batches are produced. This proactive approach reduces material waste and energy consumption, leading to significant cost savings.
Improved Production Efficiency
The real-time feedback provided by a titanium dioxide density meter allows for immediate process adjustments, reducing downtime and increasing throughput. For instance, installing a density sensor before the storage tank or filtration unit enables operators to fine-tune suspension concentration within seconds. This capability is particularly valuable in high-volume production facilities, where even minor delays can impact profitability.
Compliance with Industry Standards
TiO2 manufacturers must adhere to strict regulatory standards. Inline density monitoring ensures compliance by providing traceable data on process parameters. This transparency is crucial for audits and certifications, enhancing the manufacturer’s reputation and market trust.
Implementation Strategies for Inline Density Monitoring
Choosing the Right Installation Point
Selecting the optimal installation point for a titanium dioxide density sensor is critical for effective monitoring. Two primary locations are recommended:
Before the Storage Tank: Installing a density meter before the storage tank ensures that the TiO2 suspension entering the tank meets the required density specifications. This setup is ideal for maintaining consistency during the initial collection phase, preventing issues downstream.
At the Filtration Stage: Placing a density monitor at the filtration stage allows for precise control during the drying process. This ensures that the suspension’s density remains stable, reducing the risk of filter clogging and ensuring uniform drying.
Choosing between these locations depends on the specific production setup and process requirements. For instance, facilities with complex coating processes may prioritize pre-storage monitoring, while those focused on filtration efficiency may opt for post-treatment installation.
Selecting the Appropriate Density Meter
When selecting a titanium dioxide density monitor, manufacturers should consider factors such as accuracy, durability, and maintenance requirements. Vibrating tube meters are ideal for high-precision needs, while ultrasonic sensors suit non-invasive applications. Coriolis meters are best for facilities requiring simultaneous density and flow measurements. Additionally, ensure the device is compatible with the abrasive nature of TiO2 suspensions, with materials like ceramic sensors for ultrasonic models to prevent wear.
Integrating with Process Control Systems
To maximize the benefits of inline density monitoring, integrate the titanium dioxide density meter with existing process control systems. This allows for automated adjustments based on real-time data, reducing manual intervention and improving efficiency. For example, connecting the density sensor to a programmable logic controller (PLC) enables dynamic concentration adjustments, ensuring consistent product quality throughout the production cycle.
FAQs
How to Control the Inline Concentration of Titanium Dioxide Solution?
Controlling the inline concentration of a titanium dioxide solution requires a reliable titanium dioxide density monitor. Devices like vibrating tube or ultrasonic density meters provide real-time data, allowing operators to adjust parameters such as water content or solid concentration. By integrating these meters with automated control systems, manufacturers can maintain optimal density levels, ensuring consistent product quality and minimizing waste.
What Are the Benefits of Using a Titanium Dioxide Density Sensor?
A titanium dioxide density sensor offers multiple benefits, including real-time monitoring, high accuracy, and durability in abrasive environments. These sensors reduce manual sampling errors, lower operational costs, and enhance product quality by ensuring consistent density during post-treatment. Their low-maintenance design also minimizes downtime, making them a cost-effective solution for TiO2 manufacturers.
Which Type of Density Meter Is Best for TiO2 Production?
The best titanium dioxide density meter depends on the specific application. Vibrating tube meters offer high precision for critical processes, ultrasonic sensors are ideal for non-invasive monitoring, and Coriolis meters provide dual density and flow measurements. Manufacturers should evaluate their process requirements, such as pipe size and suspension characteristics, to select the most suitable device.
Inline density monitoring is a game-changer for TiO2 manufacturers aiming to optimize their post-treatment processes. By leveraging a titanium dioxide density meter, titanium dioxide density sensor, or titanium dioxide density monitor, producers can ensure consistent quality, reduce costs, and enhance production efficiency. These tools provide real-time insights into the density of titanium dioxide solution, enabling precise control over critical stages like surface coating and filtration.
For manufacturers seeking to stay competitive, investing in advanced density monitoring solutions is a strategic move. Contact us today to explore how our cutting-edge density monitoring systems can transform your TiO2 production process and drive measurable results.
Post time: Jun-27-2025