The synthesis of formaldehyde, a vital process in industries, demands precise control over the inline concentrations of methanol and formaldehyde to ensure product quality, operational efficiency, and regulatory compliance. Formaldehyde, produced through the catalytic oxidation of methanol, is a key component in resins, adhesives, plastics, and pharmaceuticals, but even slight deviations in methanol concentration or formaldehyde concentration can lead to polymerization, reduced yields, or non-compliance with strict safety standards.
Methanol concentration sensors, formaldehyde concentration meters, formaldehyde concentration monitors, and formaldehyde concentration analyzers provide real-time, accurate monitoring, enabling plant operators to maintain optimal reaction conditions and minimize costly inefficiencies.
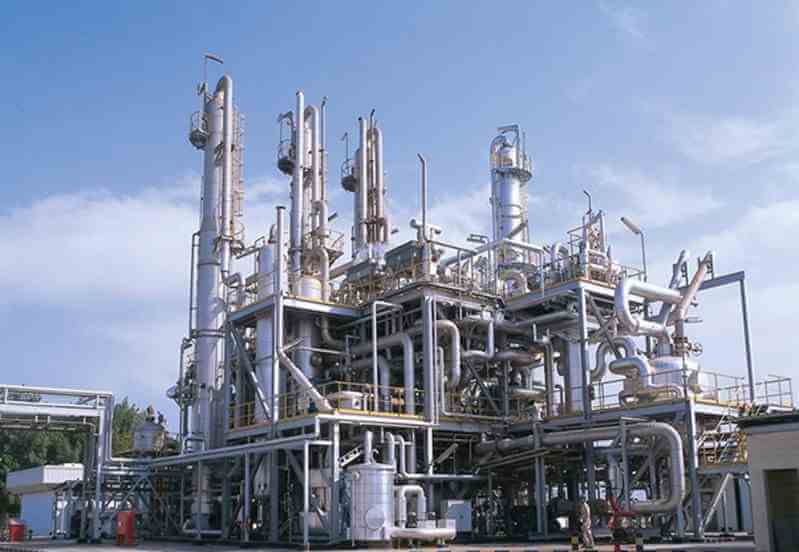
General Introduction of Chemical Process
Formaldehyde, a versatile chemical used in everything from wood adhesives to pharmaceutical intermediates, is produced through the catalytic oxidation of methanol in formaldehyde production plants. Maintaining consistent methanol concentration and formaldehyde concentration is critical to meet stringent quality standards.
Methanol concentration sensors and formaldehyde concentration analyzers are indispensable tools for achieving this precision. These devices provide real-time data, eliminating the delays and errors associated with manual sampling, and enable operators to optimize reaction conditions, reduce waste, and ensure compliance with environmental and safety regulations.
The Chemistry and Process of Formaldehyde Synthesis
The synthesis of formaldehyde involves the catalytic oxidation of methanol, a process that has been refined over decades to meet the demands of industries like chemical manufacturing and pharmaceuticals. This exothermic reaction is catalyzed by either silver or iron-molybdenum, with methanol vapor mixed with air and passed over the catalyst in a reactor.
The resulting formaldehyde is absorbed into an aqueous solution, often stabilized with 10–15% methanol to prevent polymerization to paraformaldehyde. The process requires precise control of methanol concentration in the feedstock and formaldehyde concentration in the reactor and final product to ensure high yields.
Key stages include:
Methanol Preparation
Ensuring the feedstock has the correct aqueous methanol concentration (typically 50–60 wt%) to optimize reaction efficiency.
Oxidation
Controlling the methanol-air ratio and reactor conditions to maximize formaldehyde production and minimize byproducts like formic acid.
Absorption
Absorbing formaldehyde into water to form formalin, requiring accurate formaldehyde concentration measurement to prevent polymerization.
Storage and Stabilization
Adding methanol stabilizers to maintain formaldehyde concentration and prevent degradation.
Why Inline Concentration Control is Critical
Maintaining precise methanol concentration measurement and formaldehyde concentration measurement is critical for several reasons. Excessive methanol in the feedstock can lead to incomplete oxidation, reducing formaldehyde yields and increasing waste. Conversely, insufficient methanol can starve the reaction, lowering productivity. In the absorption stage, high formaldehyde concentrations (above 50 wt%) risk polymerization, forming paraformaldehyde solids that clog equipment and disrupt operations.
Traditional monitoring methods, such as offline gas chromatography or titration, are time-consuming and prone to errors, delaying corrective actions. Methanol concentration sensors and formaldehyde concentration monitors provide continuous, real-time data, enabling operators to adjust feedstock ratios, reactor conditions, and stabilizer additions instantly, ensuring consistent product quality and operational efficiency.
Recommended Lonnmeter Inline Concentration Monitor
The Lonnmeter ultrasonic concentration meter operates by measuring the transmission time of ultrasonic waves from a signal source to a receiver, inferring the speed of sound to calculate density and concentration. This method is unaffected by bubbles, foam, or the liquid’s conductivity, color, or transparency, ensuring high reliability in challenging environments like formaldehyde production plants.
The absence of moving parts eliminates mechanical wear, guaranteeing consistent performance over time. The meter’s non-intrusive design minimizes maintenance, and its corrosion-resistant materials withstand aggressive chemicals, making it suitable for pharmaceutical plants handling formaldehyde and methanol solutions.
Installation and Integration Strategies
To maximize the effectiveness of formaldehyde concentration analyzers, strategic installation is essential. Methanol concentration sensors should be placed in feedstock lines to ensure consistent input quality, while formaldehyde concentration meters are ideal for reactor outlets and absorption columns to monitor product formation and stabilization. Redundant systems can be deployed to maintain continuous operation during maintenance, minimizing downtime.
Integration with plant control systems allows for automated adjustments, such as regulating methanol feed rates or stabilizer additions, based on real-time data. Regular calibration with standard solutions ensures measurement accuracy, particularly in the dynamic conditions of formaldehyde synthesis.
Benefits of Lonnmeter Inline Concentration Meter
Enhancing Operational Efficiency
The adoption of methanol concentration sensors and formaldehyde concentration monitors significantly improves operational efficiency in formaldehyde production plants. By providing real-time data, these devices enable operators to detect and correct concentration deviations instantly, reducing the risk of process disruptions. For example, maintaining optimal aqueous methanol concentration in the feedstock prevents incomplete oxidation, maximizing yields and minimizing waste. Similarly, precise formaldehyde concentration measurement in the absorption stage prevents polymerization, reducing equipment fouling and maintenance costs.
In petrochemical plants, these tools optimize methanol usage, reducing feedstock costs, while in pharmaceutical plants, they ensure consistent intermediate quality, minimizing rework. Industry estimates suggest that inline monitoring can reduce energy consumption by up to 10% and save significant labor time by automating analysis processes.
Ensuring Product Quality and Compliance
Formaldehyde-based products, such as urea-formaldehyde resins and pharmaceutical intermediates, must meet stringent quality and safety standards. Formaldehyde concentration analyzers ensure that the final product (e.g., formalin) maintains the correct concentration (37–50 wt%) and stabilizer content, preventing degradation and ensuring performance in applications like adhesives and coatings.
Environmental regulations, driven by formaldehyde’s toxicity, require strict emission control. Inline meters help plants monitor and minimize formaldehyde emissions, reducing the risk of fines and enhancing sustainability. This is particularly critical in petrochemical plants, where large-scale production amplifies environmental impacts.
Cost Savings and Long-Term Value
The financial benefits of formaldehyde concentration meters are substantial. By automating monitoring, these devices reduce labor costs associated with manual sampling, potentially saving hours daily in large-scale operations. They also minimize waste by preventing over- or under-dosing of methanol and stabilizers, optimizing feedstock usage. Energy savings are achieved by maintaining optimal reaction conditions, reducing the need for excessive heating or cooling in reactors and absorption units.
The durability of these meters, constructed with corrosion-resistant materials, ensures long-term reliability in the harsh conditions of formaldehyde synthesis. Their low maintenance requirements and integration with control systems make them a cost-effective investment for chemical manufacturing plants and petrochemical plants seeking to enhance profitability.
Selecting the appropriate methanol concentration sensor or formaldehyde concentration analyzer requires careful consideration of factors like accuracy, temperature, installation method, materials, etc.
FAQs
How Do Methanol Concentration Sensors Enhance Formaldehyde Synthesis?
Methanol concentration sensors provide real-time monitoring of feedstock quality, ensuring optimal methanol concentration measurement for efficient catalytic oxidation. This prevents incomplete reactions and maximizes yields in formaldehyde production plants, enhancing product consistency.
What Are the Benefits of Formaldehyde Concentration Analyzers?
Formaldehyde concentration analyzers ensure precise measurement results formaldehyde concentration, preventing polymerization and ensuring compliance with regulatory limits. They reduce waste and improve efficiency in chemical manufacturing plants and pharmaceutical plants.
Can Inline Concentration Meters Withstand Formaldehyde Synthesis Conditions?
Modern formaldehyde concentration monitors are designed to operate reliably under the high temperatures and corrosive conditions of formaldehyde synthesis. Constructed with robust materials, they ensure long-term performance and accurate monitoring.
Methanol concentration sensors, formaldehyde concentration meters, monitors, and analyzers are essential for controlling inline concentrations in formaldehyde synthesis, enabling formaldehyde production plants, chemical manufacturing plants, petrochemical plants, and pharmaceutical plants to achieve operational excellence. By providing real-time, accurate data, these tools optimize reaction conditions, reduce waste, and ensure compliance with stringent safety and environmental standards. Ready to enhance your formaldehyde production process? Contact lonnmeter to explore advanced concentration meters tailored to your needs, unlocking efficiency and quality in your operations.
Post time: Jun-27-2025