In the fierce competition of petrochemical and chemical industries, vacuum distillation columns, the core separation equipment, have influences on production capacity, product quality, and costs of a company through operational efficiency and control precision. Fluctuations in feed density or separation efficiency lead to increased possibilities of batch failure and inefficient operation.
In the process of vacuum distillation under reduced pressure, inline density meters are employed in the product testing after distillation and separation in typical. They are commonly installed at the bottom outlet of the column, near the side draw-off point, or at the top reflux pipeline. Their primary purpose lies in real-time monitoring over density, enabling precise control of the separation efficiency and product quality in distillation while optimizing operation efficiency and labor costs.
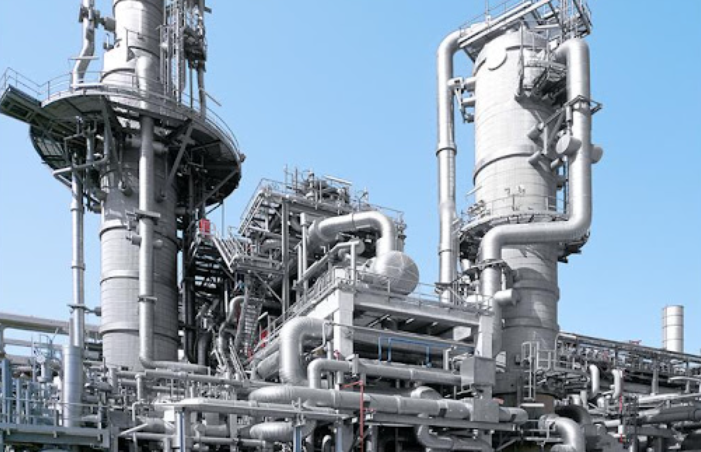
1. Challenges in Traditional Density Control
1. Equipment Idling Due to Delayed Testing
In traditional manual sampling and analysis, obtaining density data from a vacuum distillation column takes 20–60 minutes. The gas-liquid phase separation state inside the column could not measured and controlled. If feed density fluctuates or separation efficiency drops, the reflux ratio or heating power fail to be adjusted in time. Then it results in increased risks of batch failure and inefficient operation.
2. Defective Quality Caused by Manual Errors
Errors of density meter measurements by manual titration or in laboratory go up to ±5%, which fails to meet the precision requirements for high-purity products such as aviation kerosene or pharmaceutical-grade solvents. For instance, the lubricant base oils deviation of 0.01 g/cm³ may result in viscosity non-compliance and even reprocessing of the entire batch.
Even worse, failure in monitoring aqueous phase density can cause incidents that products features a certain content of oil, triggering to system shutdown of downstream water treatment and even safety & environmental risks.
3. Cost Traps Cumulative Hidden Losses
Labor costs of manual sampling may require 2–3 dedicated personnel working in three shifts, with annual labor costs exceeding $300,000. Density fluctuations cause component separation errors, wasting hundreds of tons of crude oil annually. Frequent adjustments in process parameters shorten the lifespan of the column and reboiler, increasing maintenance costs by 15%–20%.
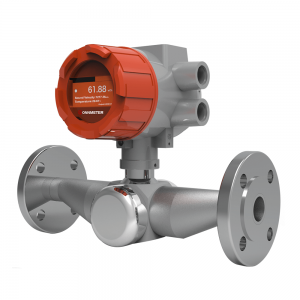
2. Introduction of Intelligent Inline Density Meter
Taking the Lonnmeter inline density meter as an example, ultrasonic density meters measure the propagation time of sound waves to calculate sound velocity, from which liquid concentration or density is derived. This technology can display suspension density, with an accuracy of ±0.0005 g/cm³ and rapid response times, completely revolutionizing traditional monitoring methods.
1. Real-Time Monitoring Throughout the Whole Process
Feed End: Installing a density meter in the pipeline before crude oil enters the vacuum column enables real-time tracking of feed density fluctuations (e.g., during co-refining of heavy and light crude oils). It integrates with the Distributed Control System (DCS) to automatically adjust vacuum settings and column top cooling loads, ensuring stable distillation efficiency.
Separation End: A density meter at the oil phase outlet dynamically monitors distillate oil density. When values deviate from the target (e.g., 0.85 g/cm³ ± 0.005), it automatically adjusts the reflux ratio to minimize quality losses.
Drainage End: Setting a density threshold (e.g., 0.9 g/cm³ triggers an alarm) at the aqueous phase outlet prevents oil carryover, reducing downstream wastewater treatment loads and raw material waste.
2. Short-Term Investment & Long-Term Value
1. Cost Savings
Labor Costs: Eliminating dedicated sampling personnel saves $250,000–400,000 annually.
Raw Material Costs: Improved density control reduces crude oil consumption by 0.3%–0.5%. Take 1 million tons processing as a example, cost savings in raw materials go beyond $5 million.
Energy Costs: Automated control reduces equipment downtime, lowering steam consumption by 8%–12%, saving $1–1.5 million in energy costs annually.
2. Efficiency Improvements
Single distillation cycles are shortened by 10%–15%, which is equal to annual capacity of a small-to-medium-sized distillation column.
Batch-to-batch density variation drops from 3.5% to 0.8%, significantly enhancing customer trust in high-end products.
3. Compliance and Safety Enhancements
-Meets ISO 9001 quality management system and OSHA safety standards, providing a complete real-time data traceability chain for FDA, EPA, and other regulatory audits.
Non-contact measurement avoids human exposure to high-temperature, high-pressure media, reducing risks of burns or poisoning and aligning with modern ESG (Environmental, Social, Governance) requirements.
When it refers to precision of industrial production, the inline density meter is not a monitor merely but a critical hub combining real-time date and process optimization. For companies pursuing intelligent transformation, choosing an inline density meter means restructuring production logic with precise readings, seizing a competitive edge in industry reshuffling.
Obtain a customized density monitoring solution to make your vacuum distillation column a benchmark for efficiency in the era of smart factory! Click to contact us and unlock the core competitiveness.
Post time: Jun-04-2025