Density-mass per unit volume is an essential metric in the complex world of material characterization, being an indicator of quality assurance, regulatory compliance and process optimization in aerospace, pharmaceutical and food industries. Seasoned professionals excel in choosing appropriate strategy and instruments for direct and indirect density measurement.
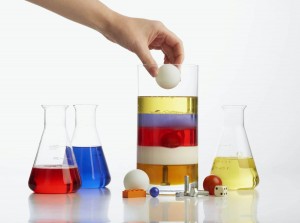
Mastering Direct Density Measurement
It's simple to get the density value by dividing a sample’s mass by its volume (Density = Mass/Volume) in direct density measurement. The method appeals to whom prefer tangible and hands-on processes. Volume of items are determined through geometrical calculations, in which submersion in a graduated cylinder reveals the displaced volume.
The approach shines in density calculation of metal components or plastic parts in manufacturing industries. The allure of direct measurement lies in its accessibility. Therefore, professionals are allowed to get accurate density values without breaking banks of items. Nevertheless, irregular shapes confound geometric calculations while tiny samples push the boundaries of standard equipment precision.
Sophistication of Indirect Density Measurement
Just as its name implies, density values inferred through properties that correlate with it, avoiding direct mass and volume measurements. The advantages of indirect density measurement lie in its versatility. In other words, tricky problems came across in density measurement are overcome through ultrasonic and radiation-based approaches.
Indirect density measurement matters in real-time monitoring to improve efficiency. However, their sophistication comes at a cost—specialized instruments like pycnometers or densitometers demand significant investment, and their operation often requires skilled technicians and meticulous calibration to maintain accuracy.
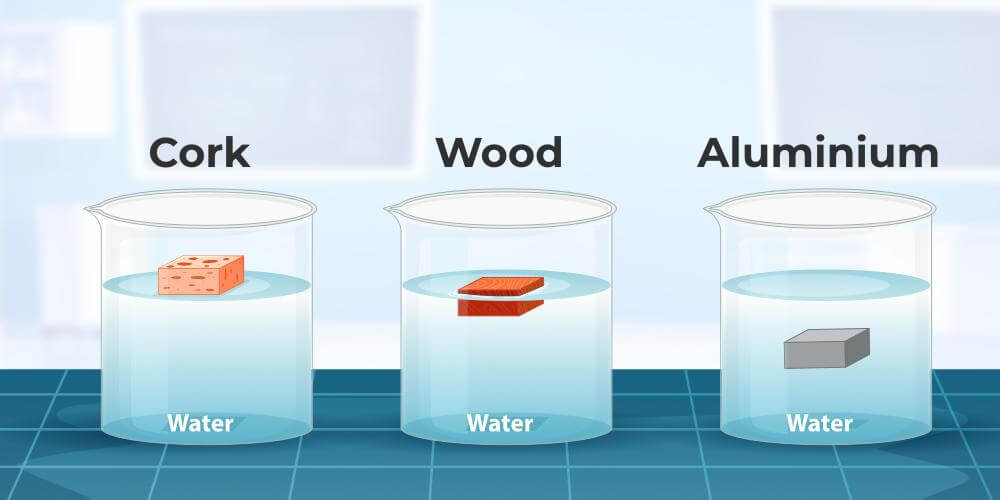
Dissecting the Core Differences
Direct measurement is rooted in physical quantification of mass and volume for tactile and intuitive process; indirect measurement depends on secondary phenomena like buoyancy, resonance or radiation, in which a deeper understanding of material interactions is required to push the boundaries of accuracy.
Direct methods reply on measurement tools in laboratories while indirect methods require advanced process sensors like tuning fork density meters or densitometers tailored to specific applications but carry heftier price tags.
For uniform solids or liquids, direct measurement delivers pinpoint accuracy with minimal fuss. Indirect methods shine with complex samples—powders, foams, or gases—though their precision hinges on rigorous calibration and operator expertise.
Direct measurement suits straightforward tasks, like quality checks in food production or educational experiments. Indirect measurement dominates specialized arenas, such as pharmaceutical powder analysis or petroleum density profiling, where sample complexity reigns.
Strategic Selection for Your Operations
Make a strategic decision between direct and indirect measurement according to specific applications, budgets and operational constraints. The affordability and ease make the former a no-brainer for oversea of small-scale manufacturing or educational labs.
On the contrary, professionals in pharmaceuticals, aerospace, or energy sectors, grappling with powders, composites, or fluids, will find indirect methods indispensable. Talk with our engineers to ask assistance in selecting appropriate density measurement instruments.
Post time: May-08-2025