Metal surface preparation requires precise control over concentration in alkali degreasing bath, in which rust and paint will be removed easily even in hard to reach areas. Precise concentration is a guarantee of effective metal surface cleaning and preparations, operational efficiency and regulatory compliance.
Alkali concentration meters and acid alkali concentration meters provide real-time monitoring to maintain optimal chemical balances in aqueous alkaline degreasing processes, critical for industries like metal surface preparation, metal fabrication and machining, and industrial parts cleaning.
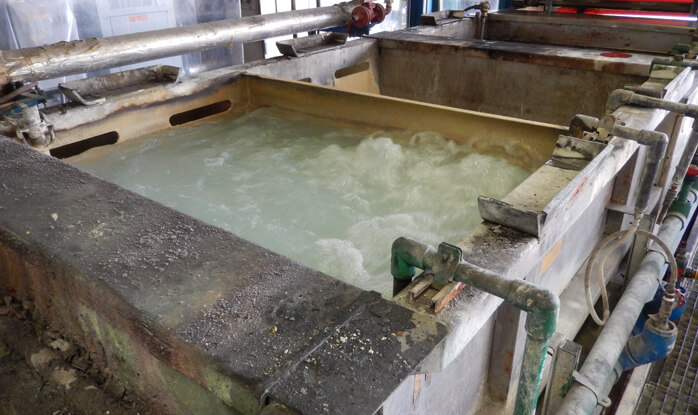
Importance of Alkali Concentration in Degreaser Production
Alkali concentration measurement is the backbone of effective aqueous alkaline degreasing, where solutions like sodium hydroxide (NaOH) or potassium hydroxide (KOH) remove oils, greases, and contaminants from metal surfaces. Deviations in alkali concentrations can cause incomplete degreasing, leading to defective coatings or welds, or overly aggressive solutions that corrode delicate components. Acid alkali concentration meters provide real-time data to maintain optimal concentration, ensuring consistent performance across batches.
For instance, alkali concentrations between 2-10 wt% ensures thorough cleaning without damaging substrates. For metal fabrication and machining, precise alkali concentration prevents residue buildup, enhancing part quality. In industrial parts cleaning, stable concentrations in the alkaline degreasing bath reduce rework and ensure compliance with environmental regulations.
Challenges of Traditional Concentration Monitoring
Traditional methods like titration for alkali concentration measurement are labor-intensive and prone to delays. Manual sampling fails to capture real-time fluctuations in alkaline degreasing baths, especially under varying temperatures or contamination levels. These methods increase operational costs and risk non-compliance with safety standards. Inline alkali concentration meters address these issues by offering continuous monitoring, enabling rapid adjustments to maintain optimal alkali concentration.
Key Measuring Points in Alkaline Degreasing Bath
Inlet of the Degreasing Bath
Monitoring the alkali concentration of the incoming degreasing solution ensures it meets the required specifications (typically 2-10 wt% for NaOH or KOH) before entering the bath.
Main Degreasing Bath
The core cleaning zone, where parts are immersed or sprayed, requires continuous monitoring to maintain stable alkaline degreasing bath conditions during industrial parts cleaning.
Recirculation Loop
In continuous degreasing systems, the recirculation loop recycles the alkaline degreasing bath solution, requiring monitoring to maintain consistent alkali concentration and prevent degradation.
Rinse Tank Interface
Monitoring the interface between the degreasing bath and rinse tanks prevents alkali carry over, which can contaminate rinse water and affect downstream processes like coating or plating.
Waste Treatment System
Monitoring alkali levels in waste streams from the alkaline degreasing bath ensures proper treatment before discharge, supporting environmental compliance.
Recommended Inline Alkali Concentration Meters
Explore the selection of inline concentration meters to find the suitable one for your industrial automation process.
The Lonnmeter 600-4 inline concentration meter operates on a sophisticated principle, utilizing a sound wave frequency signal source to excite a metal tuning fork, causing it to vibrate freely at its center frequency. This frequency correlates directly with the density of the liquid in contact with the fork. By analyzing this frequency, the meter accurately measures liquid density, which is then used to calculate alkali concentration after temperature compensation to eliminate system drift. The concentration measurement is derived from the relationship between liquid density and concentration at a standard 20°C, ensuring precise and reliable results.
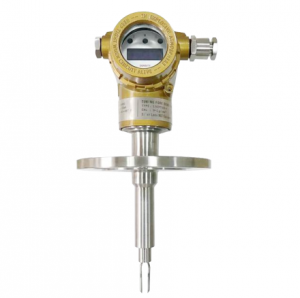
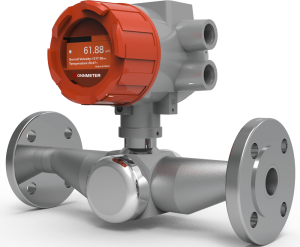
The Lonnmeter inline ultrasonic concentration meter revolutionizes real-time concentration measurement for slurries and liquids across industries. This meter measures the speed of sound by calculating the transmission time of sound waves from source to receiver. This method ensures reliable concentration measurement, unaffected by liquid conductivity, color, or transparency, making it ideal for complex alkaline degreasing baths.
Benefits of Inline Measurement
Inline acid alkali concentration meters offer real-time data for precise adjustments, reduces chemical waste and rework. Furthermore, being compliant with environmental safety regulations by continuous concentration monitoring.
Applications in Industrial Automation Process
Alkali Concentration in Metal Surface Preparation
In metal surface preparation, aqueous alkaline degreasing removes contaminants before coating or welding. Maintaining an alkali concentration of 5-8 wt% ensures effective grease removal without etching sensitive metals like aluminum. Alkali concentration meters provide continuous monitoring, adjusting chemical dosing to maintain stability. For example, a steel fabrication plant using an ultrasonic acid alkali concentration meter reported a 12% reduction in defective coatings due to precise control, saving $40,000 annually in rework costs.
Alkali Concentration in Industrial Parts Cleaning
Industrial parts cleaning relies on stable alkaline degreasing baths to clean complex components. Fluctuations in alkali concentration can lead to residue buildup, affecting part performance. Inline concentration meters ensure consistent alkali levels, reducing cleaning cycles by 15% and improving throughput. A case study in an automotive parts factory showed that real-time monitoring cut chemical consumption by 8%, enhancing sustainability.
Alkali Concentration in Metal Fabrication and Machining
In metal fabrication and machining, alkali concentration measurement prevents over-degreasing, which can damage precision components. Inline meters maintain concentrations within tight tolerances (±0.1 wt%), ensuring high-quality outputs. A machining facility integrating inline concentration monitors achieved a 10% increase in tool life by avoiding corrosive alkali levels.
FAQs About Alkali Concentration Measurement
What is the process of alkaline degreasing?
The alkaline degreasing process involves a saponification reaction, where animal and vegetable fats, oils, or greases on a surface are heated and reacted with an aqueous alkaline solution (typically sodium hydroxide (NaOH) or potassium hydroxide (KOH)) to form water-soluble soap.
How Do Alkali Concentration Meters Improve Degreaser Production?
Alkali concentration meters ensure precise control of alkali levels in aqueous alkaline degreasing, enhancing cleaning efficiency and reducing waste. They provide real-time data to maintain optimal alkali concentration, improving quality in metal surface preparation.
How Can Inline Meters Reduce Costs in Degreaser Production?
Real-time alkali concentration measurement minimizes chemical overuse and rework, saving 5-10% on material costs. In metal surface preparation, automated adjustments reduce labor and downtime, boosting profitability.
Alkali concentration measurement is vital for producing high-quality alkali degreasers, ensuring efficiency and compliance in aqueous alkaline degreasing, metal surface preparation, metal fabrication and machining, and industrial parts cleaning. By adopting acid alkali concentration meters and inline concentration monitors, alkaline degreaser suppliers and factories can optimize emulsion concentration measurement, reducing costs by up to 10% and enhancing product consistency.
These technologies address how to optimize emulsion concentration measurement in production of alkali degreaser, delivering real-time control and sustainability. Contact us for customized alkali concentration meter solutions or visit our website for a free consultation today!
Post time: Jul-11-2025